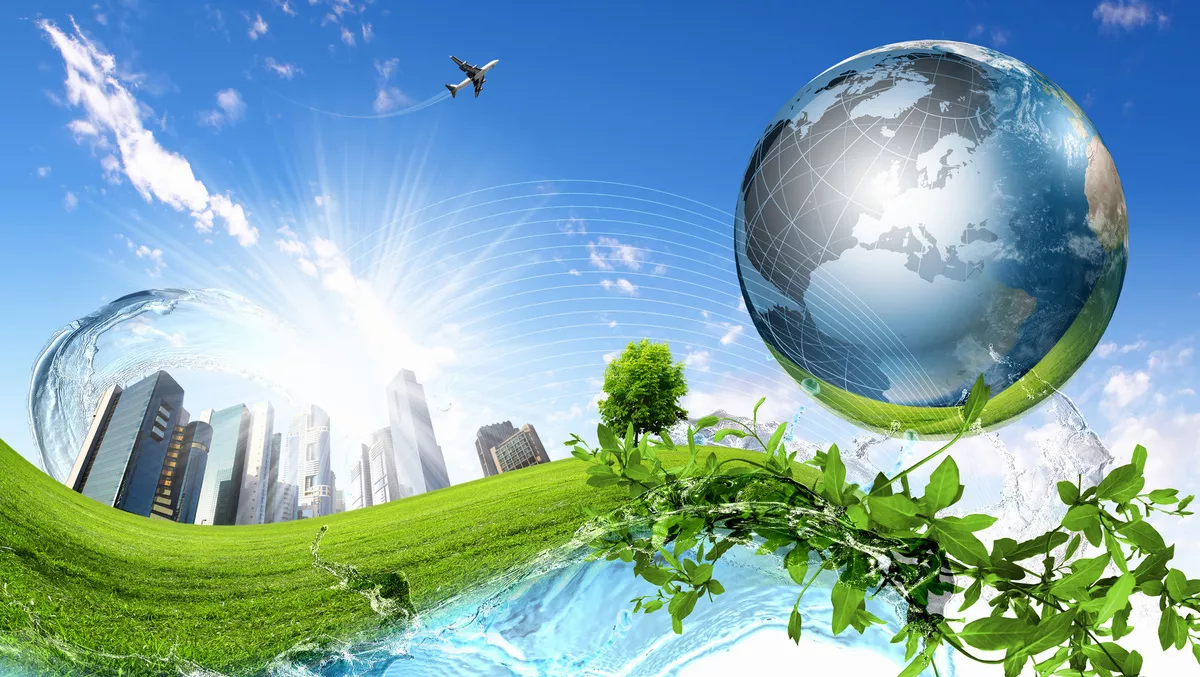
Developing the sustainable data center of the future
The global data center sector is estimated to account for around 416 terawatts, equivalent to roughly 3% of all energy needs. Southeast Asia draws a significant amount of that requirement, with energy demand increasing as new data center infrastructure is added in countries across the region.
Concerns about the environmental impact of data centers have encouraged some countries and city-states to impose restrictions on the construction of new facilities. Singapore, for example, paused new data center development in 2019. Now that moratorium has come to an end – but new data centers can only be built if they are 'best in class in terms of resource efficiency'.
The pressure to improve the environmental performance of data centers is not only coming from governments and regulators. Hyperscale data center operators such as Google (Alphabet), Apple, Facebook (Meta), Amazon, and Microsoft (GAFAM) are increasingly looking to improve. Last year, Google set a goal to power all its cloud data centers with carbon-free energy 24 hours a day by 2030.
But what does this move towards cleaner and more sustainable facilities mean for equipment such as diesel generators?
It should be noted that data center generators are not big emitters of carbon emissions, as they are used infrequently and then only for short periods. However, there is still an expectation for diesel generators to improve environmental performance via engine optimization, less regular on-site testing and the addition of exhaust gas after-treatment and biofuels.
Establishing a sustainability roadmap
Broadly speaking, data centers in Southeast Asia comprise three main energy groupings – on-site generation or utilities; facility systems such as cooling and electrical distribution; and IT systems. Improvements in each of these areas can contribute significantly to improved sustainability.
Generators fall into the first group, representing mission-critical on-site generation, mainly from diesel but sometimes from gas. Tier 1 data center operators in countries such as Singapore, South Korea, and Japan are specifying higher power-rated generators to help them achieve operational efficiencies and lower costs.
4MW diesel gensets have delivered much of the back-up power required. They provide a highly reliable response to electricity failure from the local transmission grid. The larger power nodes pack high performance into a small footprint – critical when space is at a premium. Also, diesel is commonly available in most regions and can be stored safely on-site, while generator spares and servicing can be readily arranged.
This mission-critical role means they are called into use infrequently, limiting the emission of carbon dioxide. That said, manufacturers are acutely aware of the need to continually improve environmental performance, resulting in significant engine optimization.
For example, KOHLER generators have been carefully designed to meet all relevant emissions standards in Southeast Asia and across other vital regions, including Europe and the US. This compliance is achievable using highly optimised internal engine design and after treatment.
Advances in generator maintenance
Most diesel generator operators will be familiar with the problem of "wet stacking", a build-up of unburned fuel in the exhaust system that result in decreased engine performance and premature failure – and can also lead to the breaching of emissions regulations. This primarily occurs when generators frequently operate with little or no load because the data center generator is improperly sized for the power required or because adequate load is not always available during the exercising period.
The most effective means of avoiding wet stacking during monthly exercise is to operate the generator at the recommended minimum loading. But because data center operators do not wish to transition to building load, the monthly practice requires the use of a load bank, which can be used to supplement or perform loaded maintenance activities. This load-bank testing acts as a means of artificially boosting the load placed on the generator to burn the accumulated build-up.
Many facilities conduct load-banking according to maintenance regimes that were created many years ago. Modern diesel engine designs now use several technologies that boost operating efficiency and narrow the gaps between pistons and rings where unburnt fuel can be allowed to escape. In combination with advances such as common rail systems, this advance enables lower exercise loading by containing combustion gases and facilitating a shaped charge to be created.
The savings from switching from monthly to annual loaded testing are significant. For example, a 3250-kilowatt running a load banking cycle for 30 minutes each month burns around 660 gallons of diesel fuel and emits 186 pounds of pollutants per year. In contrast, the same monthly exercise unloaded consumes less than 300 gallons per year, and total pollutant emissions are cut by around 82% on a pounds per year basis.
Renewable biofuels enter the mix
Another area of environmental advance comes with adopting the latest renewable fuels such as hydrotreated vegetable oil (HVOs) – typically comprising paraffinic bio-based liquid fuels produced from existing farm-based feedstocks, including rapeseed, sunflower, and soybean oil. These are straight-chain hydrocarbons free of aromatics, oxygen, and sulphur, and can deliver high cetane numbers.
Importantly, HVOs represent a simple and efficient renewable energy solution and are up to 90% carbon neutral. They can be stored more easily than biodiesels, and they offer a 'slot-in' solution that can be used in conventional diesel engines.
It can also be blended with diesel to ease the transition. Consequently, many of Kohler's diesel industrial generators are already compatible with HVO paraffinic synthetic biofuels.
Batteries and fuel cells
But what about exciting, step-chain revolutionary solutions such as batteries and fuel cells?
Utility-scale batteries, underpinned by advances in lithium-ion technology and combined with renewable energy supply, could represent a potential solution. Some hyperscale operators are researching megawatt-scale battery systems.
Interestingly, renewables-plus-storage techniques could potentially be used for grid service applications – with on-site batteries at facilities such as data centers being used to help utility companies manage fluctuations on the grid. The challenges around battery-based systems come with issues such as reliability, quality, and cost-effectiveness, but research and development activities are underway to overcome concerns.
Hydrogen fuel cells also represent exciting technology as a solution for environmentally friendly backup power. Again, data center operators and their industrial partners are implementing proofs-of-concept with proton exchange membrane fuel cells combining hydrogen and oxygen in a process that produces water vapour and electricity. A 250-kilowatt fuel cell system was used in one trial to power a row of data center servers for 48 consecutive hours.
The challenge with hydrogen comes with scalability and cost. It is estimated that to run 30MW of IT equipment for 48 hours would require 100 tons of hydrogen. A delivery truck can carry two tons of hydrogen – so around 50 shipments would be needed for a two-day outage. But hydrogen does remain an exciting possibility, and Kohler is developing a prototype 60 kW hydrogen generator using Polymer Electrolyte Membrane fuel cell technology.
The next generation of data centers located in Southeast Asia will need to be greener and more sustainable than ever before. This shift will likely come from continued advances on multiple fronts – from new maintenance strategies and the adoption of renewable fuels to the use of advanced fuel cells and batteries to help make sure the more sustainable data center becomes a reality.
For more information on Kohler's solutions, click here.