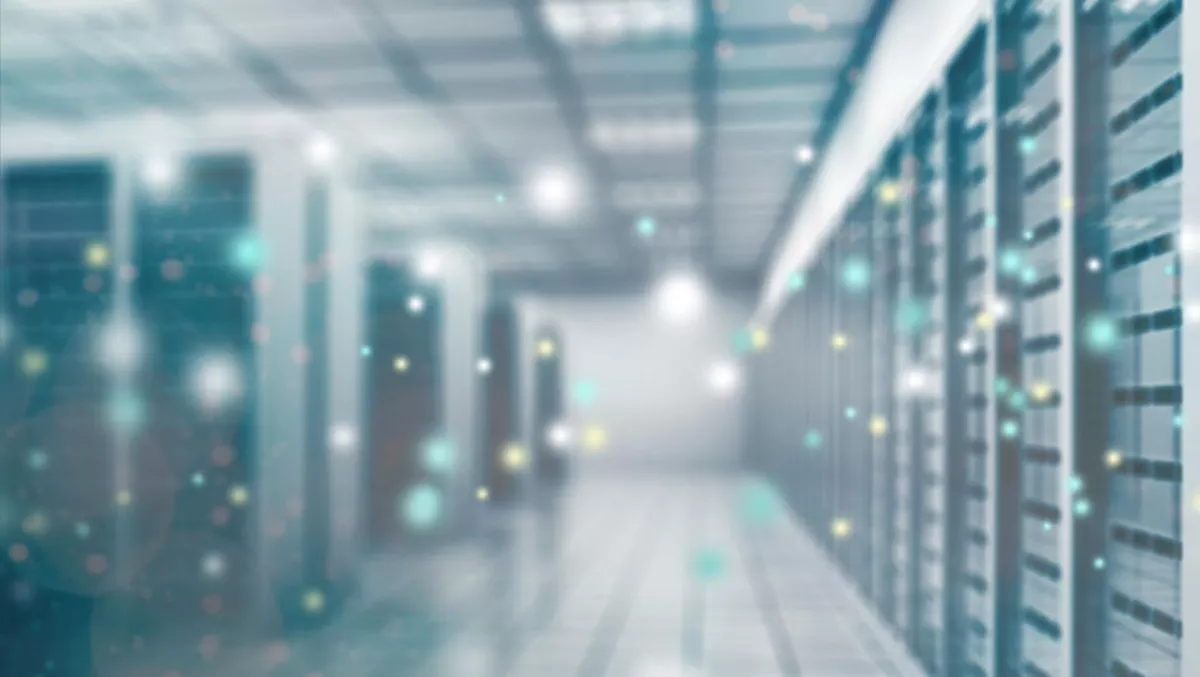
New whitepaper determines what cooling compressor matches your data centre
At the heart of a data center is its cooling infrastructure, and at the heart of that is its compression system.
Schneider Electric recently launched a new whitepaper that does what it says on the tin ('The Different Types of Cooling Compressors') in detailing which cooling compressor may be the most appropriate fit for specific data center applications.
Schneider Electric Data Center Science Center director and senior research analyst Victor Avelar says the principles are the same for your common household fridge freezer as they are for industrial-scale air conditioning in data centers.
"Inside these closed-loop systems, fluid refrigerant carries heat energy away from the cold coil (i.e. evaporator coil) to the compressor where it is condensed from a low-pressure, low-temperature vapour to a high-temperature, high-pressure liquid, before being pushed around the refrigeration loop for the purpose of heat rejection," says Avelar.
"There are many different types of compressors, however, each is appropriate for specific data center applications (area to be cooled, efficiency, power rating, and cost). A simple classification into two types, namely "constant-speed" and "variable-speed" is common practice but is not sufficient for choosing the most appropriate technology for a facility, dependent on its size.
When it comes to data centers, Avelar says the different compressor options available can be slotted into five categories, which have been illustrated in green in the table below.
The most common type of compressors used in data centers are variants of the basic positive-displacement configuration, with four of the five falling into this category.
"In positive-displacement systems, the cooling refrigerant is compressed using a chamber whose volume can change. This is typically achieved using the motion of a piston in a cylindrical chamber (single-acting)," says Avelar.
"Other compressors in the positive-displacement category are rotary compressors where compression is achieved by the rotation of a vane in a cylinder (rotary vane) or by the rotation of a scroll (rotary scroll) or two matching helical screws inside a casing (rotary screw).
While all the above are examples of positive-displacement compressors, the highest capacity, most efficient – and most expensive – is the fifth option, centrifugal models.
"In centrifugal models, cool vapour refrigerant is forced to pass into and through an impeller which forces the fluid to spin faster and faster. The high-speed gas is then forced to pass through a diffuser where the refrigerant gas expands as its speed decreases," says Avelar.
"This process converts the kinetic energy of the high-speed low-pressure gas to a low-speed higher pressure gas. The higher the impeller speed, the higher the pressure.
Reciprocating single-actingPros – wide-use in many applications, broad capacity range, relatively cheap Cons – low energy efficiency, large dimensions, inevitable wear and tear from vibration as well as other factors, susceptible to liquid slugging (where some refrigerant remains in a liquid state while the majority has been vaporised, causing wear and tear)
Rotary vanePros – higher efficiency than reciprocating single acting compressor, smaller dimensions and lighter weight, more reliable because of fewer components, reduced wear and tear due to less vibration Cons – limited to small capacities below 18kW due to structure limitations, has more components and lower energy efficiencies than other models
Rotary scrollPros – higher reliability than compressors already mentioned due to simpler structure and less components, higher efficiency due to less losses because they have no suction or discharge valves, less vibration Cons – can't match the efficiency of the last two compressor types described below, typically limited to capacities between 18 and 35kW
Rotary screwPros – larger capacity and higher efficiency than the above models due to simpler structure and fewer components, less vibration, less sensitive to liquid slugging Cons – insensitivity to liquid slugging can be a problem in the long-term, only suitable for larger applications between 70 and 637kW
CentrifugalPros – highest capacity of any of the models described here, higher efficiency, higher reliability, lower maintenance costs, compact structure and less weight per capacity Cons – expensive capital costs, impractical below 70kW and are typically used for applications requiring more than 700kW
Each of these options has its place in a data center – it just depends on your size.
"In summary, for small air-conditioning or cooling units up to about 70kW capacity, one should choose between sealed piston compressors, rotary-vane or rotary-scroll compressors," says Avelar.
"In the range between 70kW and 350kW, the choices come down to open piston compressors with multiple cylinders or rotary-screw compressors. For higher capacities above 350kW the choice is between rotary-screw and centrifugal compressors with the latter being the most practical at capacities over 700kW.
There are a number of trade-offs to bear in mind with each option, with Avelar specifically pointing out:
- Cost – piston compressors are cheaper per kW than rotary-vane compressors at low capacities
- Efficiency – centrifugal and rotary-screw models are the most efficient
- Input power per unit – piston compressors, rotary-vane and rotary-scroll are the lowest, while rotary screw and centrifugal are the highest.